"Made in Germany" stands for the highest quality worldwide, reflecting the highest standards we apply to our product solutions. The majority of our products are manufactured at our company headquarters in Ahlen, Westphalia. This approach not only conserves valuable resources by reducing long-distance transport and improving our carbon footprint, but also optimizes the entire ecological production process.
Our food supplements are produced in a facility covering 4,000 m², where products like our Aloe Vera Drinking Gels, LR Mind Master, and Vita Active are manufactured on-site. The special focus is on our aloe vera products. Products such as our Aloe Vera Drinking Gels, LR Mind Master and Vita Active are manufactured on site. In the production of aloe vera products, we prioritize gentle processing to preserve the potency and purity of the natural ingredients. Both the final products and the manufacturing process are regularly inspected by the SGS Institute Fresenius.
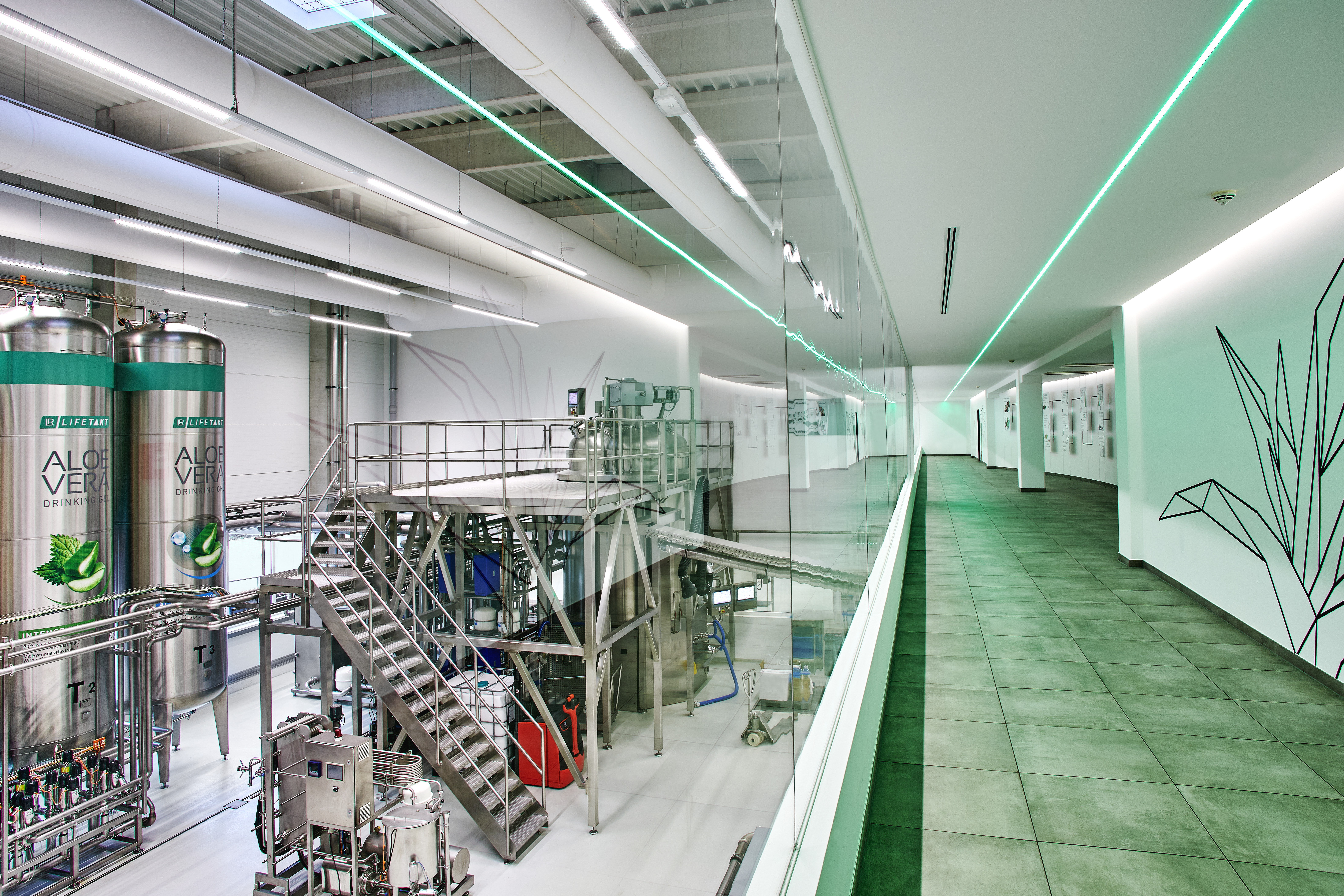
A standout feature for visitors to our health production facility in Ahlen is the Aloe Vera Production Skywalk—a 40-metre-long glass walkway that offers a live view of the entire production process, from mixing to filling and packaging. The 6.5-metre-high mixing plant and three high-tech containers, each with a 30,000-litre capacity, are particularly impressive. This is always a highlight of our visitor days for partners!
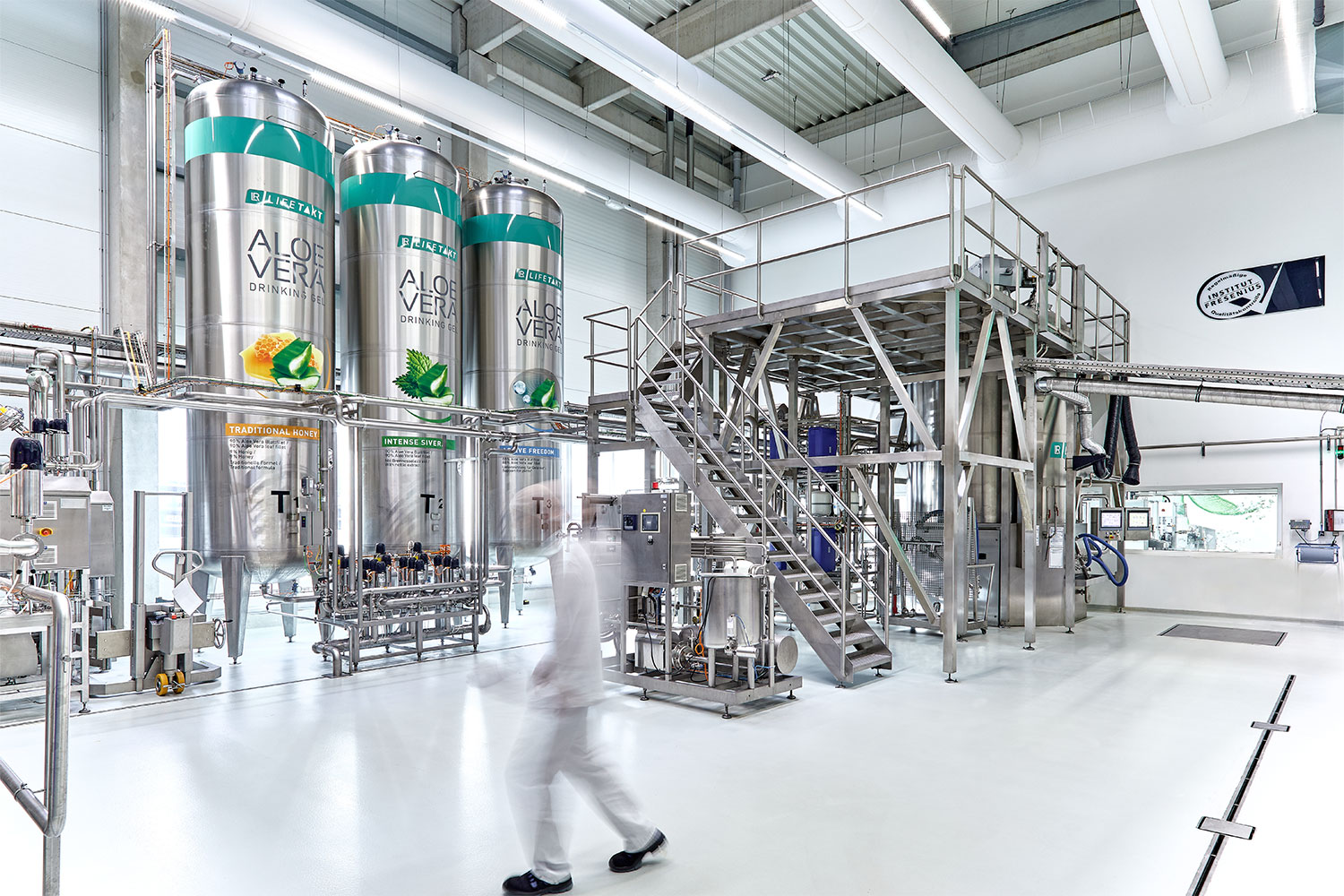
Aloe vera has been key to LR’s success and is now a cornerstone of our product range. It's no wonder that our customers and sales partners are especially passionate about our aloe vera production.
Want to learn more? Take an exclusive behind-the-scenes look now …
Care products such as our Aloe Via Aloe Vera Propolis Cream, Aloe Via Aloe Vera Emergency Spray, and Zeitgard Cleansing Cream are produced in our beauty facility, which spans 1,500 m².
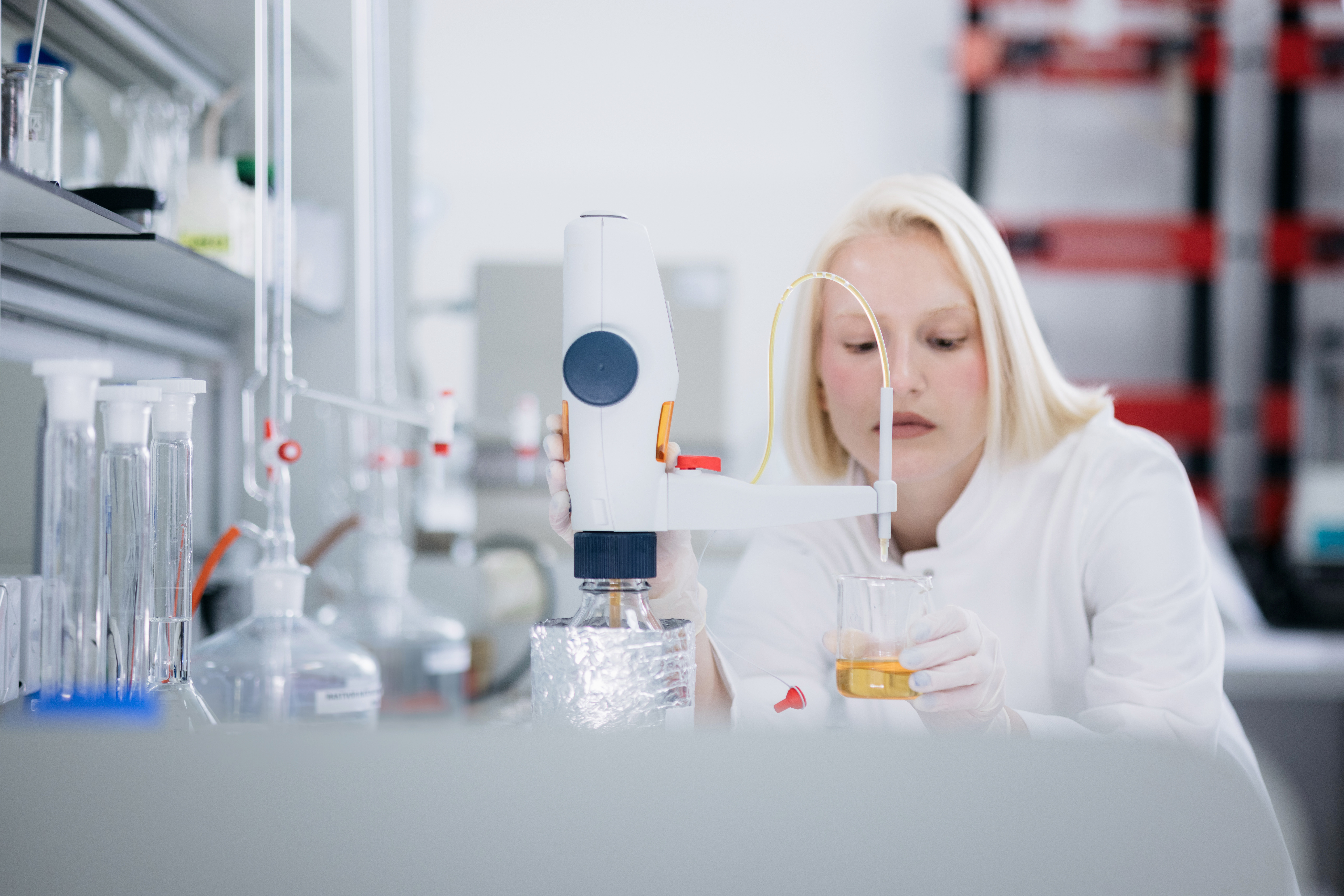
Before a finished product is sent to our customers, the raw materials undergo a standardised process: It starts with an incoming goods inspection to guarantee the quality and safety of the raw materials. Then, all ingredients are weighed in the correct quantities in the pre-weighing room and then processed. One by one, the ingredients are mixed in separate tanks and processed into a homogeneous, stable product.
During the final quality control, the quality assurance department samples the product and tests it for attributes such as appearance, odor, and chemical composition using a test catalog. If the product meets all criteria, it is approved for further processing, bottled, and stored.
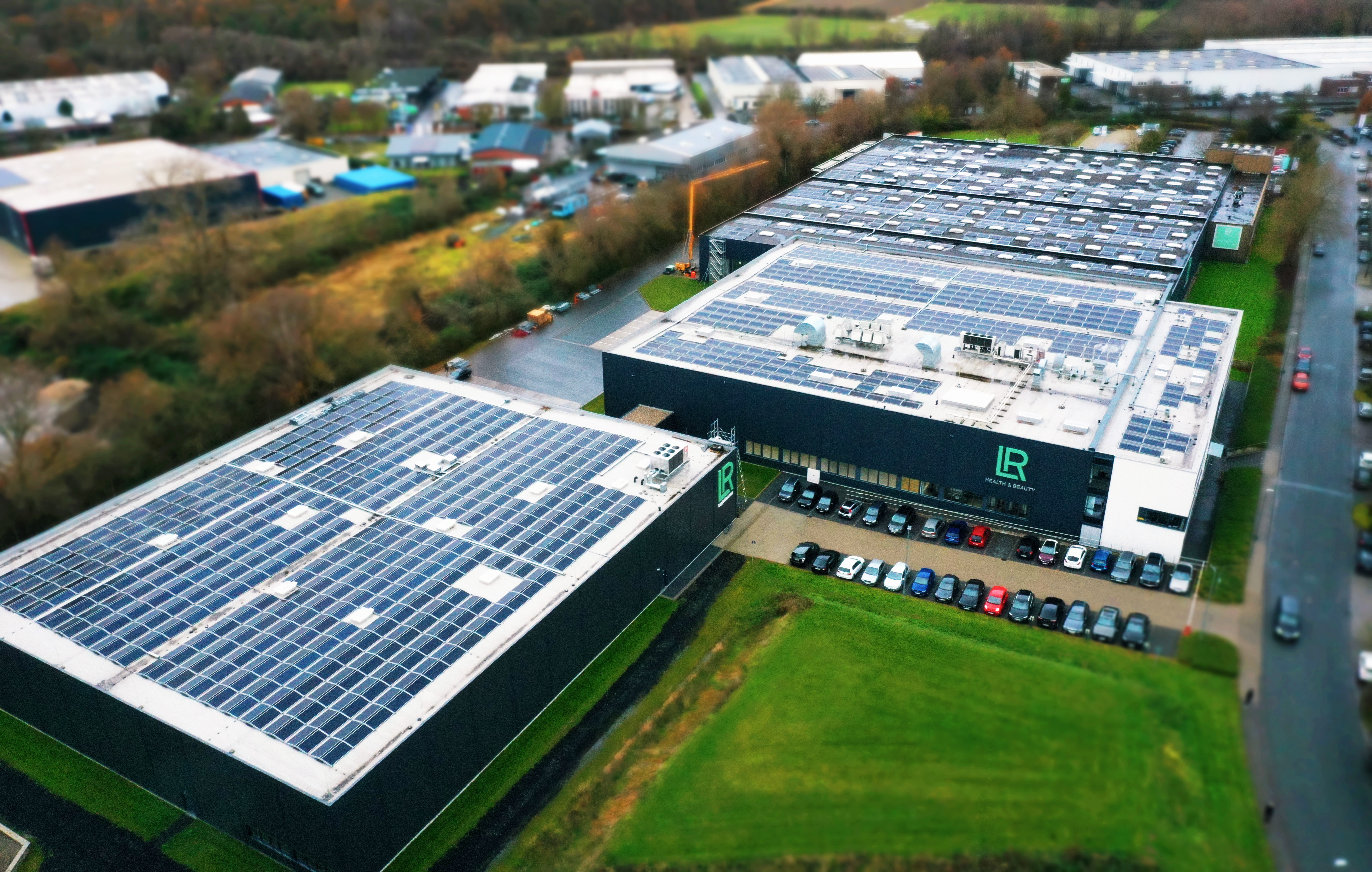
Our production is sustainable and climate-friendly. 100% green electricity is used on site in Germany. Nearly all folding cartons are made from FSC-certified paper, and some bottles and jars are crafted from recycled or plant-based plastic.
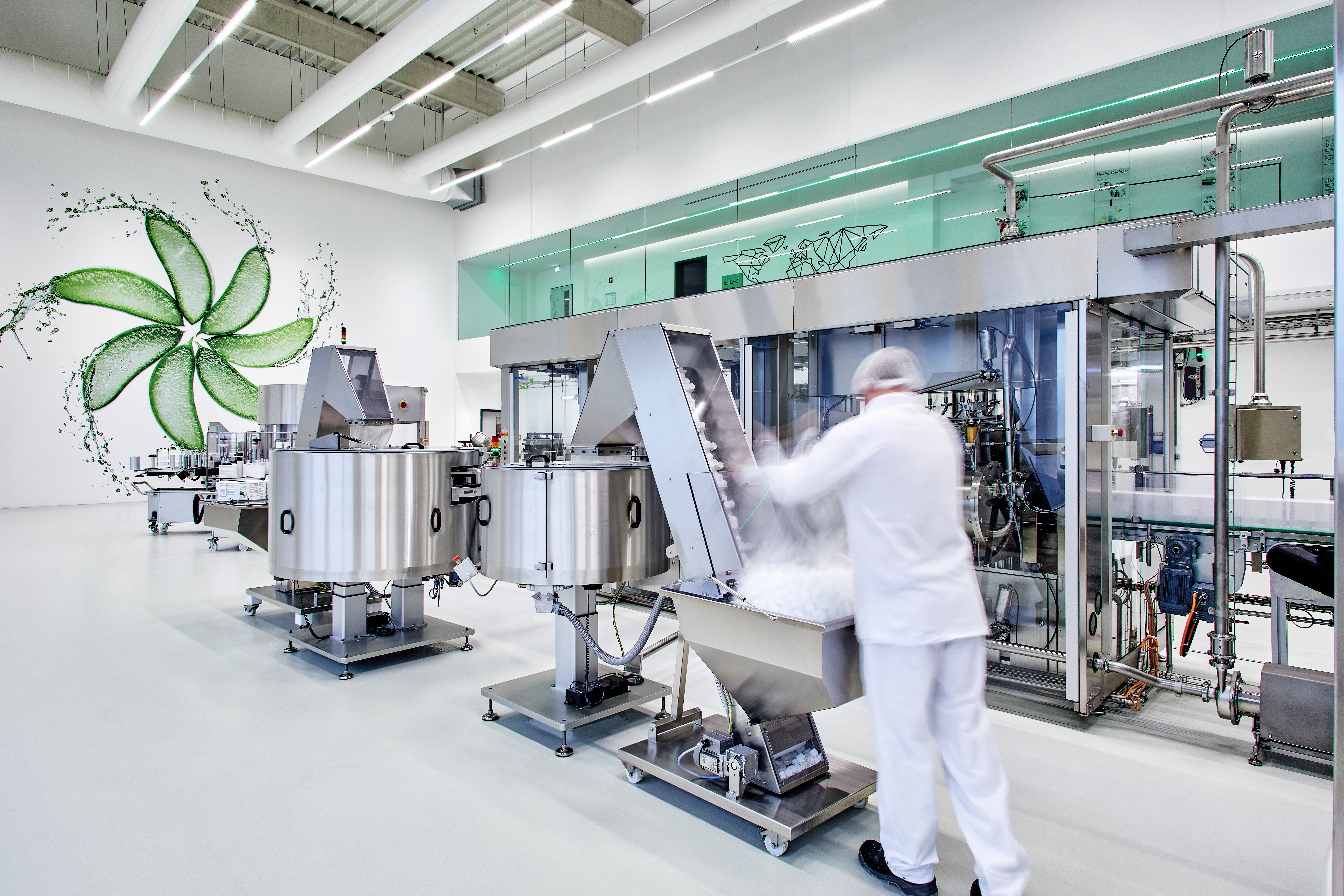
We are particularly proud of our high-tech production facilities. Our innovative, state-of-the-art machinery enhances our quality standards and establishes global benchmarks through our advanced technologies.